The Basics of Metallic Fasteners Design and Production
페이지 정보
작성자 Lionel 댓글 0건 조회 217회 작성일 25-03-28 18:08본문
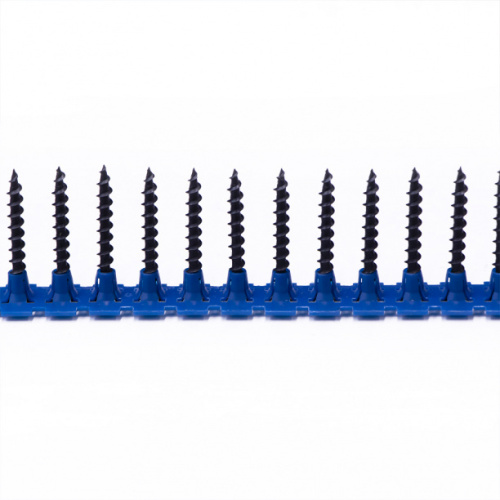
Design Considerations
In designing metallic fasteners, the following are key factors there are numerous factors that need to be taken into account including different types of materials to be joined, the load and stress the fastener will face to, and operating conditions it will operate in. The fastener should be designed to resist stress and strain and loads without collapsing and it should be compatible the component materials.
The design process typically involves several stages including initial design development, design and analysis, pre-production testing, and final quality control. CAD software is often used to create computer-aided designs of the fastener, enabling for precise engineering and quality control. The design should include various important parameters such as tensile strength, yield strength, torsion requirements, and torque requirements.
Production Methods
Steel fastener production process for metallic components involves shaping and forming the metal into the desired shape. There are several manufacturing processes that can be used, including forging, metallurgical casting, milling and drilling, and drawing. Each process has its own benefits and drawbacks, and the production method selection will depend on the type of fastener, the quantity required, and the overall expense.
Metal Forming Methods involves metallurgical forming through metal percussion or metal deformation, while casting involves depositing the liquid metal into a mold. Machining involves cutting and shaping the metal using machines, while drawing involves forcing the metal through a die to shape it.
Component Material Choice
The choice of material for the component materials is vital to performance, as it will affect the performance and reliability of the Fastener material needs to be durable and resistant and also corrosion-resistant to corrosion and wear. The iron and steel alloy with the most versatility often is the SAE J429 Grade 5 which is used for common construction.
Testing and Inspection
Following production the component products undergo quality control and evaluation to ensure they meet the required standards and specifications. The tests typically include tensile and torque tests to measure the reliability of the product. The inspection process includes visual and inspections to ensure the fastener meets the required product specifications.
Regulatory Compliance and Industry Standards
Component products are regulated to meet meet specific standards and specifications. The most common certification bodies include American Society of Mechanical Engineers, ASTM, дюбель гвоздь металлический забивной and EN. These standards guarantee the components meet specified quality, reliability, and performance standards.
Final Thoughts
Component materials creation and industrial production require careful consideration of various factors, including design, product production requirements, component specification selection, quality control processes, and industrial and regulatory compliance. By adhering to this guide, engineers and producers can create high-quality steel fasteners that meet the required specifications and performance standards.
In today's fast-paced business environment of modern construction, the importance of component products must be acknowledged. Strong, reliable connections capable of withstanding various environmental conditions can be maintained using component materials, and in an time of increasing efficiency and reliability are essential, any decision made on any fastener design must be based on comprehensive research with feasibility studies prior usage.
댓글목록
등록된 댓글이 없습니다.